
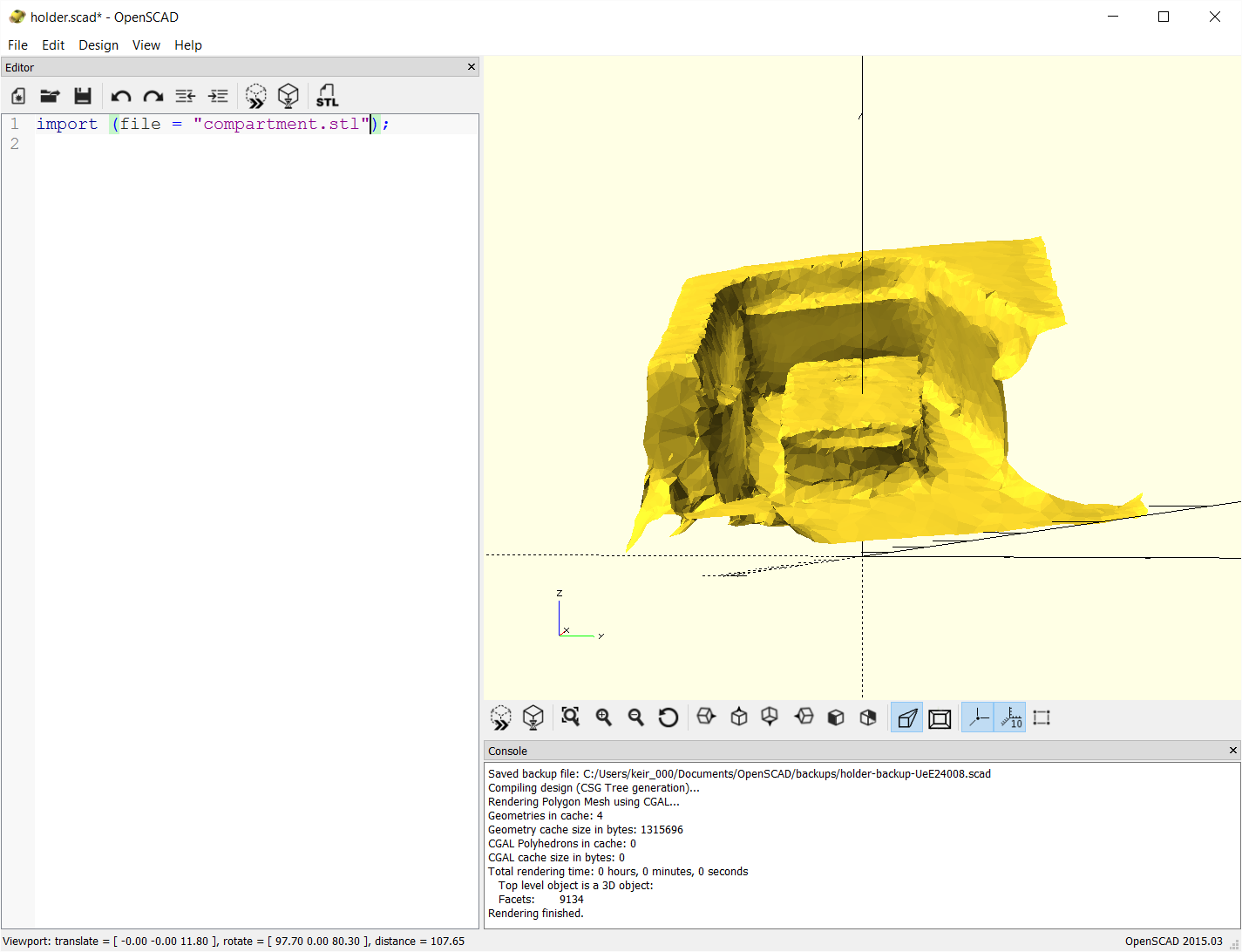

The example shows both with the small gear being the flat one. If you don’t specify this parameter you will get a flat gear for pitch angles less than 45 degrees and a back cone gear for pitch angles greater than 45 degrees. Gear_thickness: The thickness of the gear for bevel_gear_back_cone finish (see below).īacklash: Makes the tooth width smaller to make a gap between teeth of correctly spaced gears to allow for manufacturing tolerances.įinish: Specify either bevel_gear_flat(0) or bevel_gear_back_cone(1). Pressure_angle: Defines the shape of the teeth.Ĭlearance: Gap between the tip of the teeth on one gear and the root of the teeth on another meshing gear.īore_diameter: The size of the hole in the middle. Outside_circular_pitch: The circular pitch at the outside pitch diameter. Parametric Involute Profile Bevel (Conical) Gears take the following parameters:Ĭone_distance: The distance from the pitch apex to the outside pitch diameter. If this is omitted it will be 1/4 of $fn. Involute_facets: the number of facets in one side of the involute tooth shape. Hub_thickness: the thickness of the section around the bore.īore_diameter: size of the hole in the middleĬircles: the number of circular holes to cut in the gear plate.īacklash: the space between this the back of this gears teeth and the front of its meshing gear\\’s teeth when the gear is correctly spaced from it. Rim_width: radial distance from the root of the teeth to the inside of the rim. Rim_thickness: the thickness of the gear at the rim (including the teeth). Gear_thickness: the thickness of the gear plate. Pressure_angle: controls the shape of the teeth.Ĭlearance: The gap between the root between teeth and the teeth point on a meshing gear. Parametric Involute Spur Gears take the following parameters:Ĭircular_pitch or diametral_pitch: controls the size of the teeth (and hence the size of the gear). The STLs provided are not intended for direct use, but instead show examples of what can be done with the parametric script. Thanks also to elmom for some enhancements to my original gear script.Įnhancements include the Bevel gear module, backlash settings, parameterised number of facets for the involute curve and whole of tooth generation to avoid some of the issues the original script had when mirroring a half tooth.
#OPENSCAD BEVEL CODE#
It uses some of the spur gear nomenclature code from TheOtherRob with my own code for generating the involute teeth. It has some major enhancements over my original gear script. Truncate selected vertices - r determines the point of truncation.This OpenSCAD script provides modules for both Spur and Bevel Gears. 'expand and twist' - each vertex replaced by a face and each edge creates 2 triangles Replace N-face with an inset N-face and N pentagons Like kis but inset from the edge by ratio r - Conway's operator i is dkĮach N-face is divided into N triangles which extend to the face centroid moved normal to the face by hĪ face rotation that creates N quadrilaterals at an N-vertex Truncation to the edge midpoint, so each N-vetex becomes an N-face, each M-face replaced by an inscribed M-faceĮxchange vertices and faces - every vertex bceomes a face, the centroid of every face a vertexĮach N-face is divided into N pentagons composed of a vertex, two edge points and the centroid
#OPENSCAD BEVEL FULL#
Each can be parameterised, either with a single number "k5" or full parameters in parentheses "k(fn=5,h=0.5)". Conway formula either stored with the polyhedron data or entered manually allow an range of operators identified by a single lower-case (for operators) or upper-case (for primitives and decorative transforms).
